2021.01.13 WED 【挑戦する中小企業_沼津】製造業の業務改革!ワンストップ自動化ロボット開発で道を拓く。 ――フリースタイルデザインズ株式会社 鈴木一輝
text by : | 嶋崎真太郎 |
---|---|
photo : | 嶋崎真太郎 |
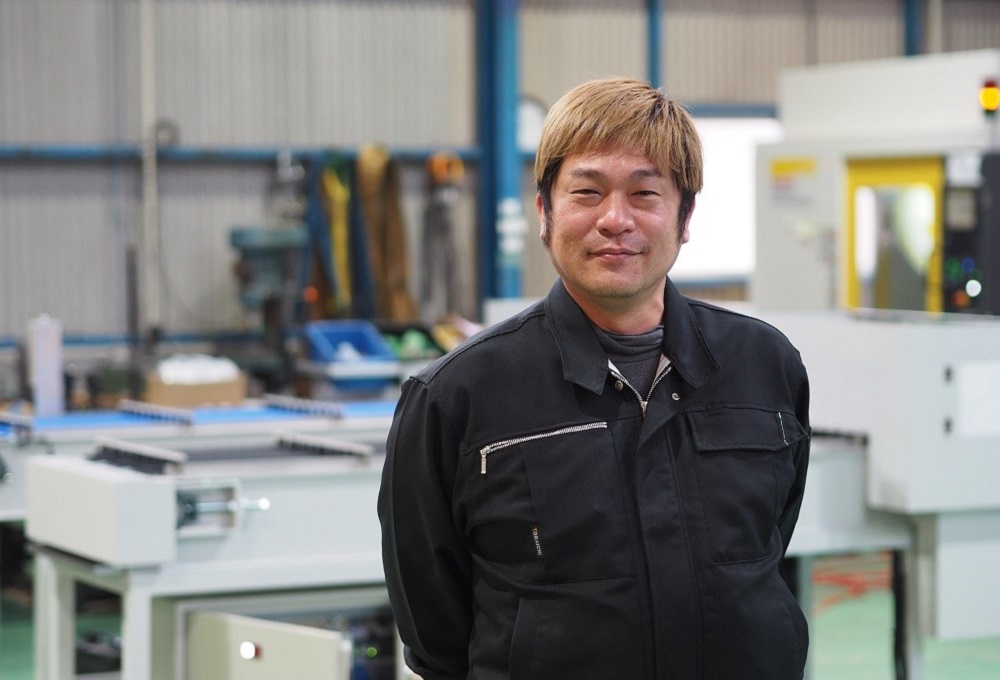
中小製造業の転換期とも言われる、第四次産業革命。超高齢化社会を目前に控え、労働人口の減少に伴い、工場の自動化が推奨されてはいますが、何から着手して良いかわからず困っている企業も多いのではないでしょうか。
フリースタイルデザインズ株式会社では、設計から開発、導入からメンテナンスまで伴走型で自動化支援を取り組んでいます。独学で3次元CADや電気工学、機械工学を学び、ロボット開発に没頭する少数精鋭の開発メーカーが目指す未来とは。代表の鈴木さんにお話を伺いました。
モノづくりの面白さに魅せられて
私は高校を卒業して、機械加工や金型加工、金型の製作会社からキャリアスタートしています。電気科を卒業しているのですが「電気好きなら、機械も覚えた方が良い」と社長から言われ、お客様から使わなくなった機械を無料でいただき、それをまず分解するところから学び始めました。プログラムもそこから抜き出し、なぜ動くのか、どういう風にできているのだろう。ひとつずつ勉強しながら覚えて行きました。
モノづくりって面白いなと思っていた先、地元の大手エレクトロニクスメーカーで中途採用の話があり入社しました。そこで高電圧のインバーターやエレベーター動力の研究開発をしていました。3次元CADにも出会ったのがこの会社です。ただ、当時を振り返ってみると、なかなか活用した事業ができなかったのを覚えています。仕事はとても楽しかったですが、自分のやりたいことに挑戦してみようとフリースタイルデザインズ(以降、FSD)を始めました。
3次元CADの活用はここからで、これまでは2次元の図面しか見たことがなかったのですが、3次元は自分のイメージをダイレクトに設計にできる点が魅力でした。学校に通った訳でもなく、誰かが教えてくれたものでもないので、独学でものすごく勉強したのを覚えています。
モノづくりというのは、自分のイメージの具現化だと思っています。頭の中のイメージが目の前で形になる、それだけでも面白いのですが、それが動くようになり製品となる、そうすると自分の開発したものが世の中に流通する。自分の設計したものが世の中に出ていて、それが人の役に立っている、使ってもらっている。それを実感しているうちに、モノづくりの楽しさに魅せられ、新しいことに挑戦することが楽しくなっているのがいまです。
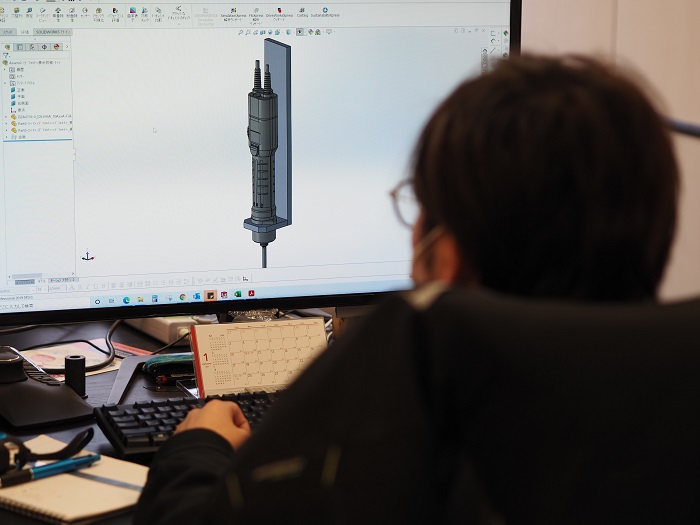
3次元CADが、モノづくりの見え方を変えた
これまでは2次元CADを使って、頭の中で3次元イメージを想像することが重要でしたが、3次元はそこがダイレクトに表現できるので、わかりやすいし設計しやすいです。ガラッと変わりました。
特に3次元で役に立っているのは、設備内の干渉している箇所や、動作エラーなどが事前にシミュ―レーションできる点です。2次元だと3次元のイメージをスタートの起点とするので、動作エラーが発生したり、予想もしなかった障害が起きたりすることがあります。
創業前に在籍していたエレクトロニクスのメーカーで、3次元CAD設計は自社では行なっていたのですが、それを外部に発注することはできませんでした。3次元CADで設計しているメーカーが当時いなかったのが理由です。昔ながらの2次元でやっていますというケースがほとんどで、これは3次元をもっと活用したいという私の想いと、自分たちがその立場になればもっと社会から必要とされる企業になるのではないかという理由で3次元CADの設計会社として創業しました。最初は設計だけでしたが、その後、設計から開発までを行なうスタイルに変わっていきました。
ワンストップ自動化ロボット開発に至った起点
ある企業との取引がきっかけでした。私たち最初は治具や預かってきたものをそのまま再現してもう一回作る等、個別の案件を中心にやっていたのですが、それが装置開発に移行していきました。知人の社長から、うちの仕事をやってみなよと、コンビナートや物流搬送系の設備を中心に事業展開しているメーカーの案件を引き受ける事になったのです。
コンビナートのような大型設備の設計はしたことはありませんでしたが、教えてもらいながら、コンベアを設計して製品作ります。というところから、そのままトントン拍子に発展していき、設備を設計しては私一人で組んで納品してというのを繰り返していました。実際、設備設計だけですと周りにも競合が複数いるので、「モノづくり×設備」で他がやっていないことをやったほうがいいだろうと、ロボット業界に入っていきました。元々ロボットには興味があったのですが、これも独学です。3次元CADを勉強した時と同様、事業に取り入れるのは大変な思いをしました。
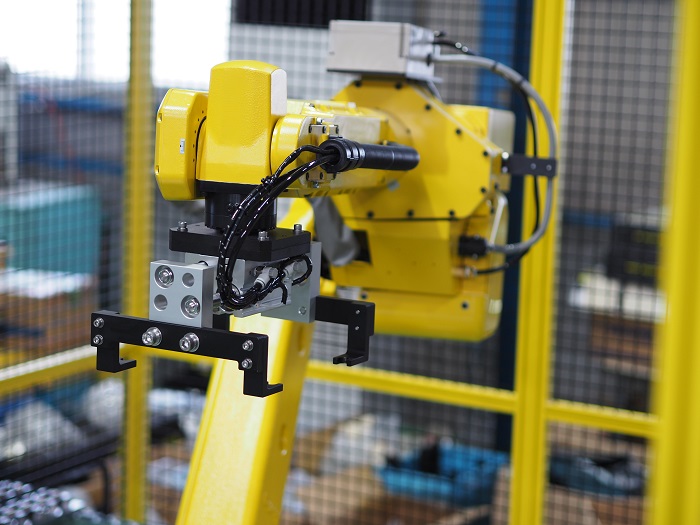
中小製造業と自動化ロボット活用の未来
自動化はしなければいけないと思っている企業様は非常に多いです。ただ、それと同じかそれ以上に「何からやればいいかわからない」という企業様も非常に多いのが実状です。ロボット導入後の事業全体像を把握できない事もありますが、自動化にかかる設備投資に莫大な費用がかかるイメージを払拭できない点で検討が進まないことが理由のひとつにもなっています。20~30名規模の中小企業規模で1,000万や2,000万、それ以上の投資を出すかというと簡単ではありません。
ですので、いきなり全て自動化に舵をきるのではなく、部分的な自動化から初めて行くことが大事だと思っています。例えば作業工程で「人が検査していて1日かかっている業務工程を数時間で処理することで生産性を伸ばしていきたい」時や、超過労働を防ぐ為に「労働時間の管理を行なう為に業務の見える化」をするなど、部分的な導入をご提案します。
また、既に自動化設備を導入されている企業様でも、最新設備のことまでは把握できないこともあります。なので、当社ではメーカーさんとの連携を密に取りながら、直接声をかけてもらうこともそうですし、展示会等を通じて最新情報を仕入れる努力は行なっています。
自動化が進んでいるようなイメージを持たれる大手企業様でも、アナログな手法で製造ラインを保っている所もありますが、少子高齢化の影響もあり、数年先の事を検討しているケースもあります。大手企業が人材不足を懸念しているので、中小企業はもっとこの問題に向き合わないといけないと感じています。
目指すは中小製造業に向けた予知保全
これからは、更にIoTを活用したいと考えています。設備に関しては使用点検前の点検項目を毎日15分や20分で、入口から出口まで作業をリアルタイムで情報を収集し、データとして残すことで稼働状態を可視化し、生産性の向上に貢献したりもできます。先端Tech系のニュースでは当たり前になっているような感じですが中小企業の導入率はまだまだ低いです。まだ紙で稼働記録を録っている所は沢山あります。自動的にログが取れるようになるだけで、そこで働く社員の方々の業務効率が改善されるのです。
設備の取り扱い説明書も、設備のタッチパネルで調べられるように改良したりすると、若手の社員でも機械を扱うことができるようになります。専門職人の業務領域に少しでも近づけることができないだろうか、そんなことをロボットを通じて提供し始めています。
あとは「IoT×機械学習×ロボット」に関してだと、ロボット内部に情報を学習させ、それを見える化することで、設備の健康状態をいつでも知れるようになる予知保全がこれからの中小製造業に必ず必要になってきます。
いきなり、製造ラインに不具合が起きると大変です。これまで中小企業の製造現場では、熟練の社員が聞こえて来る音や振動の変化で設備部品の交換等をしていましたが、到底若手社員には真似できない職人技です。この職人技でもある音を学習させ、振動を学習させ、異常予兆を事前に察知する。その機械を使うことで職人さんの業務領域を補完していくことが大事で、職人技を人材に継承させることは難易度が高いと考えています。
子どもたちに伝えたい、モノづくりの面白さ
子供たちの世代がモノづくりから離れているのは残念な気がしています。インターネットやSNSが当たり前のように使われる中で、youtuberやりたいって、私の息子も言ったりするのですが、面白い事や夢中になれる事はモノづくりの現場にはまだまだあります。
仕事を通じて困りごとを助けてあげるのが仕事なので、それが達成できるアイディアを形にして提供してあげられるモノづくりの楽しさを子供に限らずもっと多くの人に伝えていきたいですね。あとは、作っておしまい。納品しておしまい。ではなく、使い方次第で設備が生きるか死ぬか、死なせないようにはサポートをしていくことも楽しさのひとつです。
実際、最新設備を使いきれないお客さんも中にいるはいます。ロボットを導入しはいいけど、止まったままになっているとか、他社経由で導入したけれど、導入したロボットは工場の端っこにいる、とか。新しく導入しなくても良いから、止まっているロボットは活用できるということを伝えたいですし、そのロボット使って何かできないとか、実際に工場見て、ここのラインで使えそうですよとか、こういうのでも使えそうですよとか、そういう介在価値を発揮できる存在でありたいですね。
モノづくりの現場にはワクワクするものが沢山ありますから。
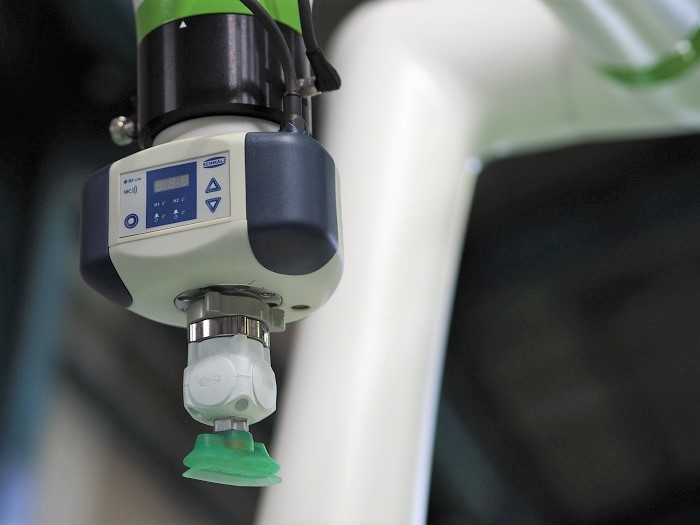
この記事に関連するページはこちら
記事はありませんでした